Gear Manufacturing Guide : Gears are the unsung heroes of the mechanical world, seamlessly driving everything from your car’s transmission to industrial machinery and even the simplest clocks. But how are these critical components made with such precision and durability?
Gear manufacturing is a fascinating field that blends engineering expertise, cutting-edge technology, and material science to create components capable of handling extreme loads, high speeds, and continuous use.
Let’s gear up and dive into the world of gear manufacturing!
What is Gear Manufacturing?
Gear manufacturing is the process of creating gears, which are mechanical components with teeth designed to transmit torque and motion between machine parts. Gears are made using various methods like casting, forging, extrusion, powder metallurgy, and blanking. While these initial processes form the basic shape, machining is typically used to achieve precise dimensions, shape, and surface finish required for optimal performance. Gear manufacturing is essential in industries like automotive, aerospace, and machinery, where gears play a critical role in efficient power transmission and motion control.
Types of Gears and Their Applications
Gears are essential components in mechanical systems, facilitating torque transfer and motion between parts. Different gear types are designed for specific applications, optimizing efficiency, noise reduction, and durability based on system requirements.
Here’s a detailed overview of the types of gears, their unique characteristics, and applications.
Here’s a detailed overview of the types of gears, their unique characteristics, and applications.
Gear Type | Definition | Applications |
Spur Gears | Spur gears have straight teeth parallel to the gear’s axis, making them the simplest gear type. They are highly efficient and easy to manufacture. | Used in low-speed, high-torque applications like conveyors, clocks, washing machines, and gear pumps. |
Helical Gears | Helical gears have angled teeth, creating a helical pattern along the gear’s face. This design provides smoother, quieter operation at higher speeds. | Common in automotive transmissions, industrial machinery, and high-speed applications. |
Bevel Gears | Bevel gears have cone-shaped teeth and are used for transferring motion between intersecting axes, usually at a 90° angle. | Found in differential drives, power plants, and hand drills for angle-shifting torque and speed control. |
Worm Gears | Worm gears consist of a worm (screw-like structure) and a worm wheel. This gear type provides high reduction ratios and self-locking properties. | Applied in elevators, conveyors, tuning instruments, and lifts due to compact size and self-locking. |
Rack and Pinion | Rack and pinion gears convert rotational motion into linear motion. The pinion engages with a linear gear (rack), moving it horizontally or vertically. | Widely used in steering systems, CNC machines, and railways for precise control of linear movement. |
Detailed Overview of Each Gear Type
1.Spur Gears
Characteristics: Simple design with straight teeth, efficient in transferring torque.
Advantages: Cost-effective, low maintenance, highly efficient at low speeds.
Drawbacks: Noisy at high speeds due to abrupt tooth engagement.
Applications: Suitable for slow-speed applications, such as conveyors, clocks, and simple mechanical devices like washing machines and gear pumps.
2.Helical Gears
Characteristics: Angled teeth that gradually engage, allowing smooth transitions and reduced noise.
Advantages: Quiet operation and capable of handling higher speeds and loads compared to spur gears.
Drawbacks: More complex and expensive to manufacture due to angled teeth.
Applications: Predominantly used in automotive transmissions, industrial equipment, and other high-speed machinery.
3.Bevel Gears
Characteristics: Teeth are cut on a cone, enabling motion transfer between non-parallel axes, often at right angles.
Advantages: Effective in changing the direction of force, versatile in applications requiring angular motion shifts.
Drawbacks: Complex to manufacture and can be challenging to align.
Applications: Found in automotive differentials, rotary machines, and tools like hand drills, where torque and speed adjustments are needed at angles.
4.Worm Gears
Characteristics: Unique design with a worm resembling a screw that meshes with a gear, providing high reduction ratios.
Advantages: Self-locking, compact, provides high torque transfer in a small space.
Drawbacks: Lower efficiency due to sliding contact, which causes frictional losses.
Applications: Commonly used in conveyor systems, elevators, tuning instruments, and jacks, where compact and high-torque systems are required.
5.Rack and Pinion
Characteristics: Consists of a circular pinion gear that engages with a linear rack, converting rotational motion to linear.
Advantages: Simple and efficient for linear motion, precise control.
Drawbacks: Limited to applications where straight-line motion is needed.
Applications: Steering mechanisms in vehicles, railways, and CNC machines for linear positioning and precise control.
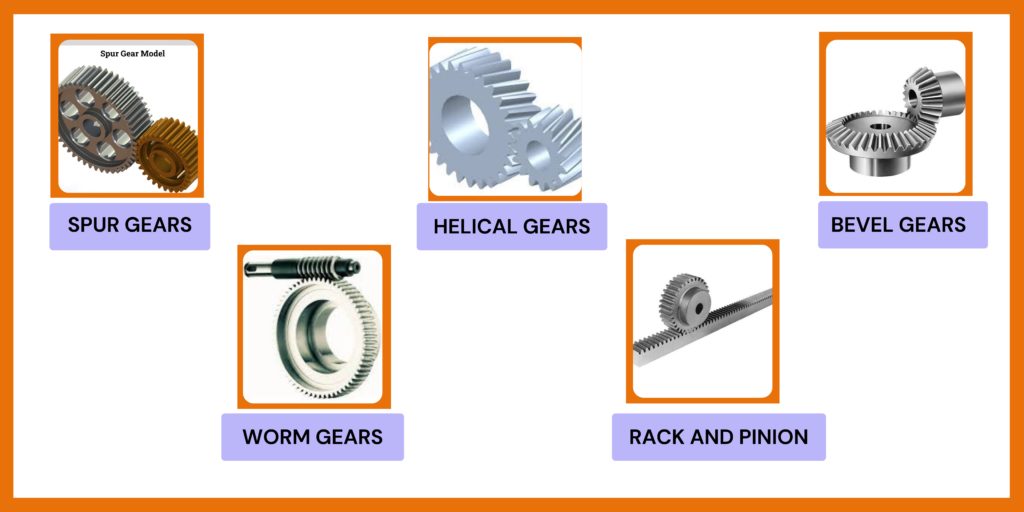
Raw Materials for Gear Manufacturing
Gears are critical components in many machines, and choosing the right material is essential to ensure they perform efficiently under specific conditions. The selection of raw materials for gear manufacturing depends on factors like strength, durability, load capacity, and wear resistance.
Here’s a look at the commonly used materials in gear production:
1. Steel
Types Used: Carbon steel, alloy steel, stainless steel
Properties: Steel is strong, durable, and highly resistant to wear and fatigue, making it ideal for high-load applications.
Applications: Automotive gears, industrial machinery, and heavy-duty applications where strength and longevity are crucial.
2. Cast Iron
Properties: Cast iron has good machinability, high damping capacity, and can handle moderate loads. It’s also more cost-effective than steel.
Applications: Commonly used in agricultural equipment, small machinery, and applications with low-to-moderate speed requirements.
3. Brass and Bronze
Properties: Brass and bronze are resistant to corrosion and have good lubricity, which helps reduce friction.
Applications: Used in marine applications, small machinery, and gears that require smooth, low-noise operation.
4. Aluminum
Properties: Aluminum is lightweight and has good corrosion resistance, but it lacks the strength of steel or cast iron.
Applications: Suitable for low-load applications, such as in lightweight machinery, robotics, and small appliances.
5. Nylon and Other Plastics
Properties: Plastic materials, such as nylon, are lightweight, have low friction, and are resistant to corrosion and moisture.
Applications: Ideal for household appliances, office equipment, and applications where quiet operation and low weight are priorities.
6. Powdered Metals
Properties: Powder metallurgy allows precise control over material composition, resulting in gears with excellent wear resistance and high strength.
Applications: Often used in automotive components and high-volume manufacturing where cost-effectiveness and precision are key.
Here’s the rewritten content with an enhanced focus on the keyword “gear manufacturing process” to improve SEO:
Step-by-Step Guide to Gear Manufacturing Processes
The gear manufacturing process is a comprehensive, multi-stage journey that transforms raw materials into precision-engineered gears designed to transmit motion and torque. This process involves shaping, cutting, and finishing techniques to ensure the correct tooth profile, dimensional accuracy, and surface finish. Below is a detailed guide to the key steps involved in the gear manufacturing process, including gear forming, form milling, and broaching.
1. Gear Forming in the Gear Manufacturing Process
Gear forming is the initial and foundational stage of the gear manufacturing process, where gear blanks are prepared to approximate the desired profile. This stage sets the groundwork for subsequent precision machining. Using tools designed to reflect the final tooth profile, the gear blank undergoes shaping that aligns with the targeted specifications.
Applications: Gear forming is critical in preparing the gear for further machining steps, ensuring structural integrity and dimensional accuracy.
2. Form Cutting in the Gear Manufacturing Process
Form cutting is a vital step in the gear manufacturing process, involving machining operations like form milling and broaching to create gear teeth. These processes cater to different gear designs, production volumes, and quality requirements.
a) Form Milling in the Gear Manufacturing Process
Form milling is a precision-driven technique in the gear manufacturing process where a form cutter is used to create the gear teeth. The cutter’s profile matches the desired gear tooth shape, ensuring accuracy.
Steps in the Form Milling Process:
- The form cutter moves axially along the gear blank, cutting at a specified depth.
- After each cut, the gear blank rotates to position the next tooth space.
- The cutter repeats the process until all gear teeth are formed.
Applications:
Form milling is widely used for producing external gears in moderate-to-high production volumes where precision is paramount.
b) Broaching in the Gear Manufacturing Process
Broaching is another essential technique in the gear manufacturing process, especially for creating internal gear teeth. It involves a broach tool with progressively larger cutting edges that gradually shape the gear teeth.
Steps in the Broaching Process:
- The broach tool is pushed or pulled through the gear blank, incrementally cutting the tooth profile.
- The gear teeth achieve precise dimensions and a fine surface finish.
Advantages:
Broaching is fast, highly accurate, and ideal for achieving a smooth finish. While it is cost-intensive due to the need for custom broaches, it is particularly effective for high-volume production.
Applications:
Broaching is extensively used in the automotive and aerospace industries, where internal gears require high precision and superior finishes.
Inspen Tech: Your Trusted Partner in the Gear Manufacturing Process
For advanced and reliable gear manufacturing processes, turn to Inspen Tech. Leveraging cutting-edge technology and industry expertise, Inspen Tech delivers custom solutions for industrial machinery, automotive systems, and specialized equipment. Our team ensures every step of the gear manufacturing process—from forming to finishing—meets the highest quality standards, resulting in durable and precise gears.
Choose Inspen Tech for unmatched accuracy, efficiency, and on-time delivery. We’re your go-to partner for all your gear manufacturing process needs.
Conclusion
The gear manufacturing process is crucial for creating the gears that power countless mechanical systems. Whether it’s gear forming, form milling, or broaching, each step is vital in producing gears that perform reliably and efficiently.
By understanding the various stages of the gear manufacturing process and selecting the right methods for specific requirements, you ensure gears contribute significantly to machinery performance and longevity. Inspen Tech stands ready to assist you in navigating the complexities of the gear manufacturing process, providing superior solutions tailored to your needs.
Approach Inspen Tech for the Best Gear Manufacturing Service
Inspen Tech offers top-tier gear manufacturing services with advanced technology, skilled expertise, and a commitment to precision. Whether you need custom gears for industrial machinery, automotive applications, or specialized equipment, Inspen Tech provides reliable solutions tailored to meet high standards of quality and durability. With a focus on accuracy and efficiency, Inspen Tech ensures your gear requirements are met seamlessly and on time. For exceptional results in gear manufacturing, Inspen Tech is your trusted partner.
Conclusion
Gears are vital components in countless mechanical systems, enabling smooth and efficient power transmission across various applications. Understanding the different types of gears—like spur, helical, bevel, worm, and rack and pinion—helps in selecting the right design for specific operational requirements.
From selecting suitable materials to choosing precise manufacturing processes like form milling and broaching, each step in gear production is crucial for achieving performance, durability, and reliability. With careful selection and quality manufacturing, gears contribute significantly to the functionality and longevity of machinery, making them indispensable in industries from automotive to aerospace.
Inspen Technology Pvt Ltd stands out among gear manufacturing companies for its innovative approach to precision engineering. As one of the leading gear manufacturing companies, Inspen Technology leverages cutting-edge machinery and advanced techniques to deliver superior-quality gears for diverse industries, including automotive, aerospace, and industrial machinery. Unlike other gear manufacturing companies, Inspen Technology prioritizes custom solutions tailored to client specifications, ensuring unmatched durability and performance. With a reputation for excellence, Inspen Technology is the preferred choice for businesses seeking reliable gear manufacturing companies for their critical operations.
FAQS
Q1: What is the standard gear material?
The standard materials for gears are steel (particularly alloy steel), cast iron, and bronze. These materials are chosen based on their strength, durability, and ability to handle varying loads.
Q2: What is the strongest material for gears?
For high-strength applications, hardened alloy steel is the strongest material commonly used for gears. Other strong materials include case-hardened steel and powdered metals, which are highly resistant to wear and fatigue, ideal for heavy-duty applications.
Q3: What is gear hobbing?
Gear hobbing is a machining process that uses a rotating cutting tool called a hob to cut teeth into a gear blank. This process is efficient and widely used for making spur and helical gears, offering high precision and productivity.
Q4: How are gears tested for quality?
Gears undergo several quality tests, including dimensional checks, surface finish inspections, and load testing. Advanced techniques, like contact pattern checks and noise and vibration testing, ensure gears meet performance standards.
Q5: What is gear backlash, and why is it important?
Backlash is the slight gap or clearance between mating gear teeth, allowing for smooth operation and accommodating thermal expansion. Controlled backlash is essential to prevent jamming and excessive wear in gears, especially in high-precision applications like robotics and automotive systems.